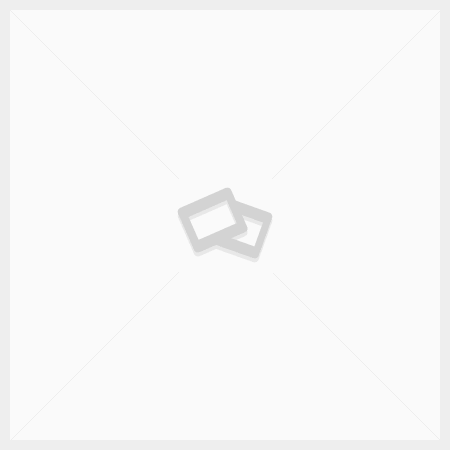
Key Facts You Need To Know About Cutting Tools
A cutting tool, also referred to as a cutter, is any tool used to remove material from a work piece, and the cutting may be done by multipoint or single-point tools.
Single-point tools are used in shaping, turning and planning and the material is removed using one cutting edge. On the other hand, in drilling and milling, multipoint tools are used.
It is essential for the cutting tools to be made of a material which is tougher than the material that is going to be cut. Ability to endure the high levels of heat generated during the metal cutting process is also important for the cutting tools.
The cutting tool must have specific geometric forms in design so that the cutting edge can contact the work piece in an effective manner during cutting, which will result in easy material removal.
The cutting tool’s clearance angles, rake angle of the cutting faces, number of teeth or flutes, and the flute width also need to meet precise measurements so that the cutter can effectively remove material from a work piece in the desired manner. The speeds and feeds at which the cutting tool is run are also important. When all these factors are put into consideration in a cutting tool, the tool can have a long working life.
There is a wide range of cutting tools, some of which are rotary and others are linear. Examples of rotary cutting tools are milling cutters, drill bits, taps and dies, and reamers, among others. Linear cutting tools comprise of broaches and single-point cutting tools.
Normally, cutting tools are designed with inserts whereby the cutting edge comprises of a separate piece of material which is clamped or brazed on to the tool body. Cutting tools that usually use inserts are saw blades, tool bits and milling cutters. The most commonly used materials for tips are tungsten carbide, high speed steel, Diamond, among others.
The important attributes which a cutting tool must have in order to produce top quality parts are as follows:
a) High levels of wear resistance, which will enable the tool to have a long working life
b) High levels of toughness, which will enable the tool to withstand a lot of pressure and energy without fracturing or chipping
c) High levels of hardness and strength
Materials used in cutting tools can be categorized into two main divisions, namely stable and unstable.
Stable materials such as tungsten carbide are materials that are consistently stable in conditions of high levels of heat which is produced by the machining conditions, and they do not change their main properties during use. These materials are naturally hard, and do not gain their hardness through heat treatment.
On the other hand, unstable materials such as steels initially have low hardness levels, and have their hardness increased through heat treatment. However while the materials’ hardness is increased during heat treatment, its toughness is compromised. The heat produced during cutting also makes these materials unstable while machining.
The main drawback for stable materials is that they are fragile. This is because they are so hard that they normally break before bending. Most tools made from stable materials have a moderately blunt edge, and this avoids chipping at the cutting edge and accounts for higher cutting forces from an increased shear area. Stable materials’ high levels of fragility and high cutting forces means these materials can be used in many applications.
Unstable materials have the advantage of being softer and therefore tougher, which enables them to bend or curve without breaking and are used in making hand tools.
Tool materials that are normally used in cutting tools include high carbon steel, high speed steel, Cemented carbide, Cermets, Diamond, Cubic boron nitride and others.
TecTools supplies turning tools, threading tools, grooving and recessing tools, boring tools, wear pads and trepan tools. We have more than two decades’ worth of experience supplying customized tools to clients from different parts of the world, and we always look forward to helping new customers by supplying them with tools that meet their specific requirements.